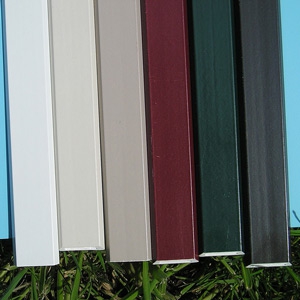
Tratamiento de superficies
El aluminio es un sustrato ideal para la aplicación de acabados arquitectónicos. Hay muchas razones para tratar la superficie.
Los atributos que pueden modificarse mediante el tratamiento de la superficie incluyen la estética, la resistencia a la corrosión, la resistencia al desgaste, la emisividad y la adhesión de otros materiales.
La superficie no tratada
Las superficies no siempre necesitan tratamiento después de la extrusión. Las estructuras portantes y las piezas de máquinas son ejemplos de productos en los que la calidad de la superficie es satisfactoria sin ningún tratamiento.
¿Por qué revestir las extrusiones de aluminio?
El aluminio se reviste por dos razones principales:
- Para controlar el aspecto para la coordinación del color, la uniformidad o el atractivo visual y para mejorar el sustrato.
- Para proteger el sustrato de los daños ambientales (por ejemplo, la lluvia ácida, la contaminación por azufre, la corrosión de la sal y la oxidación).
Procesos de recubrimiento de extrusiones de aluminio
Las extrusiones de aluminio se recubren en dos tipos de líneas, vertical y horizontal. Ambos procesos ofrecen productos recubiertos de calidad y pueden manejar una variedad de formas y tamaños. Ambos sistemas comparten las siguientes etapas básicas para el éxito de las aplicaciones de recubrimiento.
Recubrimientos líquidos
Los recubrimientos líquidos son materiales fluidos que, cuando se aplican a una superficie, forman una película adherente para proteger y embellecer el sustrato.
Los recubrimientos líquidos se componen de tres ingredientes principales:
- La resina, denominada aglutinante, es la sustancia polimérica que forma la película. El aglutinante es la espina dorsal del sistema de recubrimiento.
- Los pigmentos son las partículas que dan al recubrimiento color, poder cubriente, control del brillo y cierta protección contra la corrosión.
- Los disolventes actúan para fluidificar el recubrimiento y controlar las características de la aplicación.
Algunos recubrimientos líquidos tienen ingredientes adicionales denominados genéricamente aditivos. Estos aditivos son sustancias químicas presentes en los recubrimientos para dar un efecto especial. Pueden tener propiedades de película húmeda o seca. Las propiedades de la película húmeda incluyen la viscosidad, la formación, el desprendimiento y la estabilidad de la emulsión. Las propiedades de la película seca incluyen el brillo, el poder cubriente, el color, la resistencia y la dureza. El pigmento y el aglutinante son los componentes «sólidos» que forman la película endurecida y proporcionan las características de rendimiento requeridas. Los disolventes normalmente se evaporan por completo tras la aplicación del revestimiento. Las porciones de disolvente más cantidades menores de subproductos de la reacción química, menos cualquier agua o disolvente exento, comprenden los compuestos orgánicos volátiles (COV).
Recubrimientos en polvo
Los recubrimientos en polvo se aplican electrostáticamente desde una tolva de aire fluido.
Los ingredientes primarios del polvo son los siguientes:
- Los aglutinantes consisten en la resina, el polímero y el reticulante. Este ingrediente proporciona al polvo sus propiedades de película fundamentales.
- Los pigmentos de color primario pueden ser orgánicos o inorgánicos.
- Los aditivos cumplen numerosas funciones pero generalmente afectan a las propiedades de fluidificación y aplicación.
Para obtener más información sobre las normas de rendimiento de los revestimientos líquidos y en polvo, consulte AAMA 2603, Especificación voluntaria, requisitos de rendimiento y procedimientos de prueba para revestimientos orgánicos pigmentados en extrusiones y paneles de aluminio, AAMA 2604, Voluntary Specification, Performance Requirements and Test Procedures for High Performance Organic Coatings on Aluminum Extrusions and Panels y AAMA 2605, Voluntary Specification, Performance Requirements and Test Procedures for Superior Performing Organic Coatings on Aluminum Extrusions and Panels.
¿Qué es el anodizado?
El anodizado es un proceso electroquímico. Las formas de aluminio extruido (perfiles) se sumergen en una solución ácida bajo condiciones controladas. Una corriente eléctrica pasa a través de la solución para producir una película de óxido de aluminio en los perfiles. Esta película de óxido es extremadamente dura, duradera y resistente a la corrosión. Sirve como anclaje del color en el proceso de anodización.
Típicamente, el proceso de anodización se lleva a cabo en una serie de tanques, llenos de productos químicos de procesamiento y tanques de enjuague. Los perfiles de aluminio extruido se limpian, se graban hasta conseguir el acabado deseado y se desoxidan antes del anodizado. En la etapa de anodización, el grosor del óxido de aluminio se controla estrechamente para cumplir la especificación AAMA 611. Tras el anodizado, se pueden obtener muchos colores. El sellado completa el proceso de desarrollo de este verdadero acabado metálico. Los métodos de coloración se dividen en cuatro categorías: coloración orgánica, coloración inorgánica, coloración electrolítica y coloración electrolítica en combinación con la coloración orgánica.
Para más información sobre las normas de rendimiento del anodizado, consulte la AAMA 611, «Voluntary Specification for Anodized Architectural Aluminum» y la AAMA 612, «Voluntary Specification, Performance Requirements, and Test Procedures for Combined Coatings of Anodic Oxide and Transparent Organic Coatings on Architectural Aluminum».