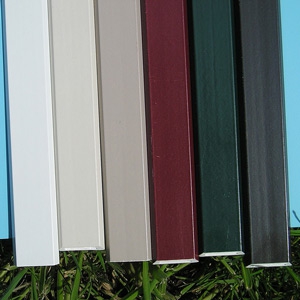
Traitement de surface
L’aluminium est un substrat idéal pour l’application de finitions architecturales. Il existe de nombreuses raisons de traiter la surface.
Les attributs qui peuvent être modifiés par le traitement de surface comprennent l’esthétique, la résistance à la corrosion, la résistance à l’usure, l’émissivité et l’adhérence d’autres matériaux.
La surface non traitée
Les surfaces ne nécessitent pas toujours un traitement après l’extrusion. Les structures porteuses et les pièces de machines sont des exemples de produits dont la qualité de surface est satisfaisante sans aucun traitement.
Pourquoi revêtir les extrusions d’aluminium ?
L’aluminium est revêtu pour deux raisons principales :
- Pour contrôler l’apparence pour la coordination des couleurs, l’uniformité ou l’attrait visuel et pour améliorer le substrat.
- Pour protéger le substrat des dommages environnementaux (par exemple, les pluies acides, la pollution par le soufre, la corrosion saline et l’oxydation).
Procédés de revêtement des extrusions d’aluminium
Les extrusions d’aluminium sont revêtues sur deux types de lignes, verticales et horizontales. Les deux procédés offrent des produits revêtus de qualité et peuvent traiter une variété de formes et de tailles. Les deux systèmes partagent les étapes de base suivantes pour des applications de revêtement réussies.
Les revêtements liquides
Les revêtements liquides sont des matériaux fluides qui, lorsqu’ils sont appliqués sur une surface, forment un film adhérent pour protéger et embellir le substrat.
Les revêtements liquides sont composés de trois ingrédients principaux :
- La résine, appelée liant, est la substance polymère qui forme le film. Le liant est l’épine dorsale du système de revêtement.
- Les pigments sont les particules qui donnent au revêtement sa couleur, son pouvoir couvrant, son contrôle de la brillance et une certaine protection contre la corrosion.
- Les solvants agissent pour fluidifier le revêtement et contrôler les caractéristiques d’application.
Certains revêtements liquides ont des ingrédients supplémentaires appelés génériquement additifs. Ces additifs sont des produits chimiques présents dans les revêtements pour donner un effet particulier. Ils peuvent avoir des propriétés de film humide ou sec. Les propriétés du film humide comprennent la viscosité, le formage, le pelage et la stabilité de l’émulsion. Les propriétés du film sec comprennent la brillance, le pouvoir couvrant, la couleur, la résistance et la dureté. Le pigment et le liant sont les composants « solides » qui constituent le film durci et fournissent les caractéristiques de performance requises. Les solvants s’évaporent normalement entièrement après l’application du revêtement. Les parties de solvant plus des quantités mineures de sous-produits de réaction chimique, moins toute eau ou solvant exempté, constituent les composés organiques volatils (COV).
Couches en poudre
Les couches en poudre sont appliquées électrostatiquement à partir d’une trémie fluidisée par air.
Les ingrédients primaires de la poudre sont les suivants :
- Les liants sont constitués de la résine, du polymère et du réticulant. Cet ingrédient confère à la poudre ses propriétés fondamentales de film.
- Les pigments de couleur primaire peuvent être organiques ou inorganiques.
- Les additifs remplissent de nombreuses fonctions mais affectent généralement les propriétés de fluidification et d’application.
Pour plus d’informations sur les normes de performance des revêtements liquides et en poudre, veuillez vous référer à l’AAMA 2603, Spécification volontaire, exigences de performance et procédures d’essai pour les revêtements organiques pigmentés sur les extrusions et les panneaux en aluminium, AAMA 2604, Spécification volontaire, Exigences de performance et procédures d’essai pour les revêtements organiques à haute performance sur les extrusions et les panneaux d’aluminium et AAMA 2605, Spécification volontaire, Exigences de performance et procédures d’essai pour les revêtements organiques à performance supérieure sur les extrusions et les panneaux d’aluminium.
Qu’est-ce que l’anodisation ?
L’anodisation est un procédé électrochimique. Les formes extrudées en aluminium (profilés) sont immergées dans une solution acide dans des conditions contrôlées. Un courant électrique traverse la solution pour produire un film d’oxyde d’aluminium sur les profilés. Ce film d’oxyde est extrêmement dur, durable et résistant à la corrosion. Il sert d’ancrage de couleur dans le processus d’anodisation.
Typiquement, le processus d’anodisation est réalisé dans une série de cuves, remplies de produits chimiques de traitement et de cuves de rinçage. Les profilés d’aluminium extrudés sont nettoyés, gravés pour obtenir la finition souhaitée et désoxydés avant l’anodisation. Lors de l’étape d’anodisation, l’épaisseur de l’oxyde d’aluminium est étroitement contrôlée afin de respecter la spécification AAMA 611. Après l’anodisation, de nombreuses couleurs peuvent être obtenues. Le scellement complète le processus de développement de cette véritable finition métallique. Les méthodes de coloration se divisent en quatre catégories : la teinture organique, la teinture inorganique, la coloration électrolytique et la coloration électrolytique en combinaison avec la teinture organique.
Pour de plus amples renseignements sur les normes de rendement de l’anodisation, consultez l’AAMA 611, » Spécification volontaire pour l’aluminium architectural anodisé » et l’AAMA 612, » Spécification volontaire, exigences de rendement et procédures d’essai pour les revêtements combinés d’oxyde anodique et de revêtements organiques transparents sur l’aluminium architectural « .